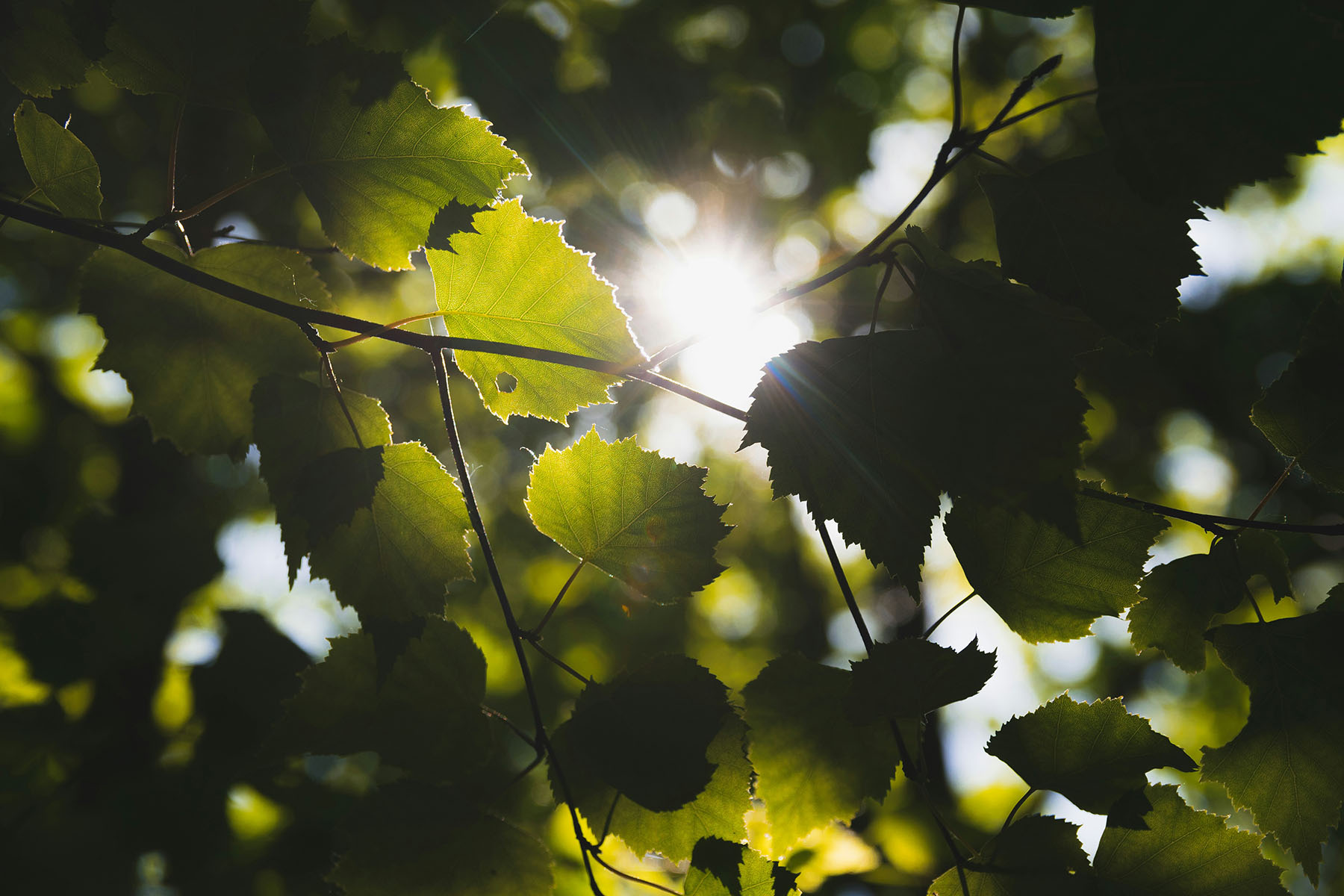
IMPROVED SUSTAINABILITY
Verified Sustainability: Over 60% Less CO₂ per Tonne of Corrugated Board
The Interpac Cold Corrugator has undergone an LCA (Life Cycle Assessment) screening by WSP in October 2024. The results are transformative for the corrugated packaging industry, revealing a remarkable 61% reduction in CO₂ emissions per tonne of corrugated board produced compared to conventional methods in the UK.
Key Drivers of CO₂ Reduction
Energy Efficiency: The Interpac Cold Corrugator operates with 41% lower energy consumption than traditional steam-based systems.
Reduced Transport Miles: By enabling in-house board production at sheet converter facilities, transport requirements are cut by 80%. Instead of transporting bulky corrugated board, which is typically 50% air, compact paper reels are moved, maximising transport efficiency.
This innovative approach not only delivers significant environmental benefits but also enhances operational efficiency, making sustainable production a viable option for sheet converters.
(Data Sources: Conventional – FEFCO 2021 LCA Report, Interpac In-house UK & DE Data, SimaPro, Ecoinvent)
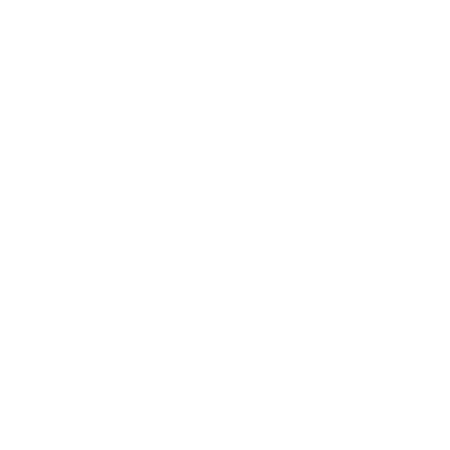
41% Less
Energy
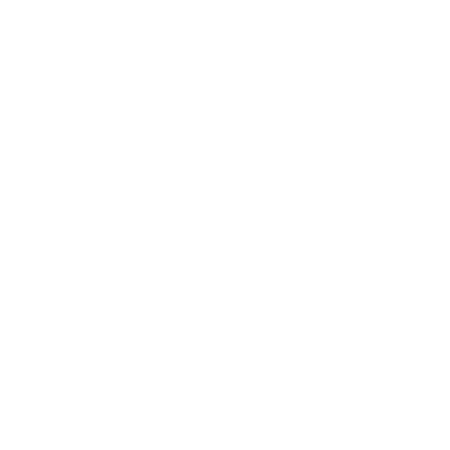
80% Less
Transport
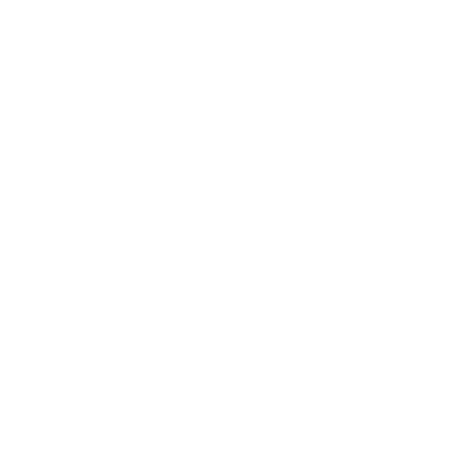
98% Less
Water
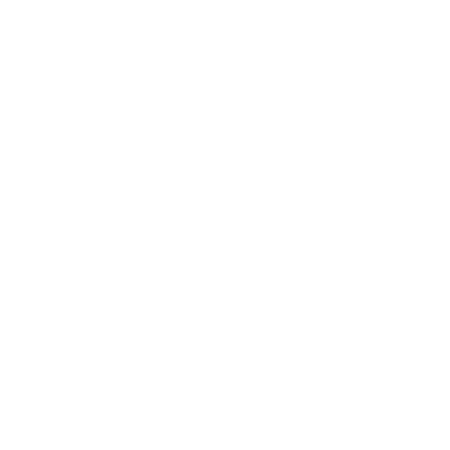
61% Total
CO2 Saving
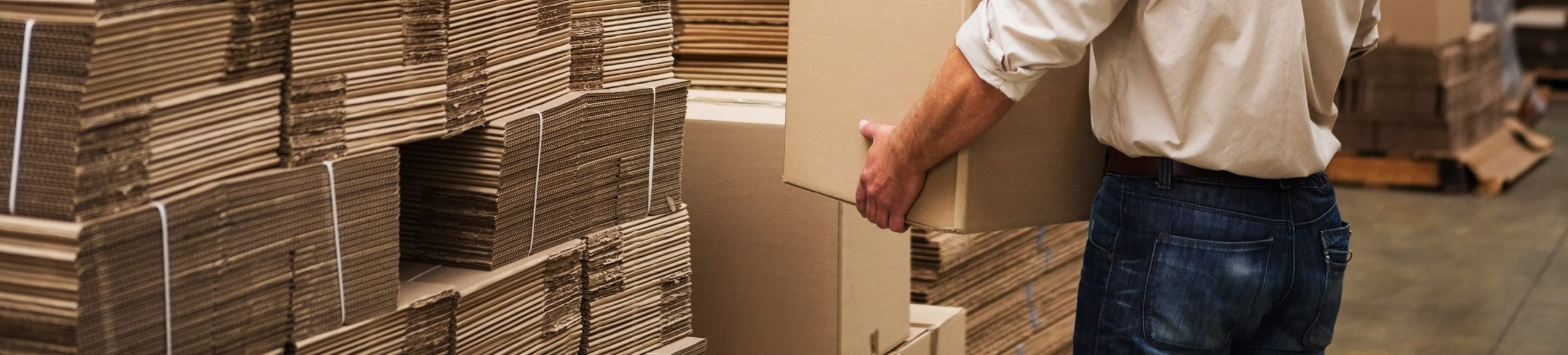