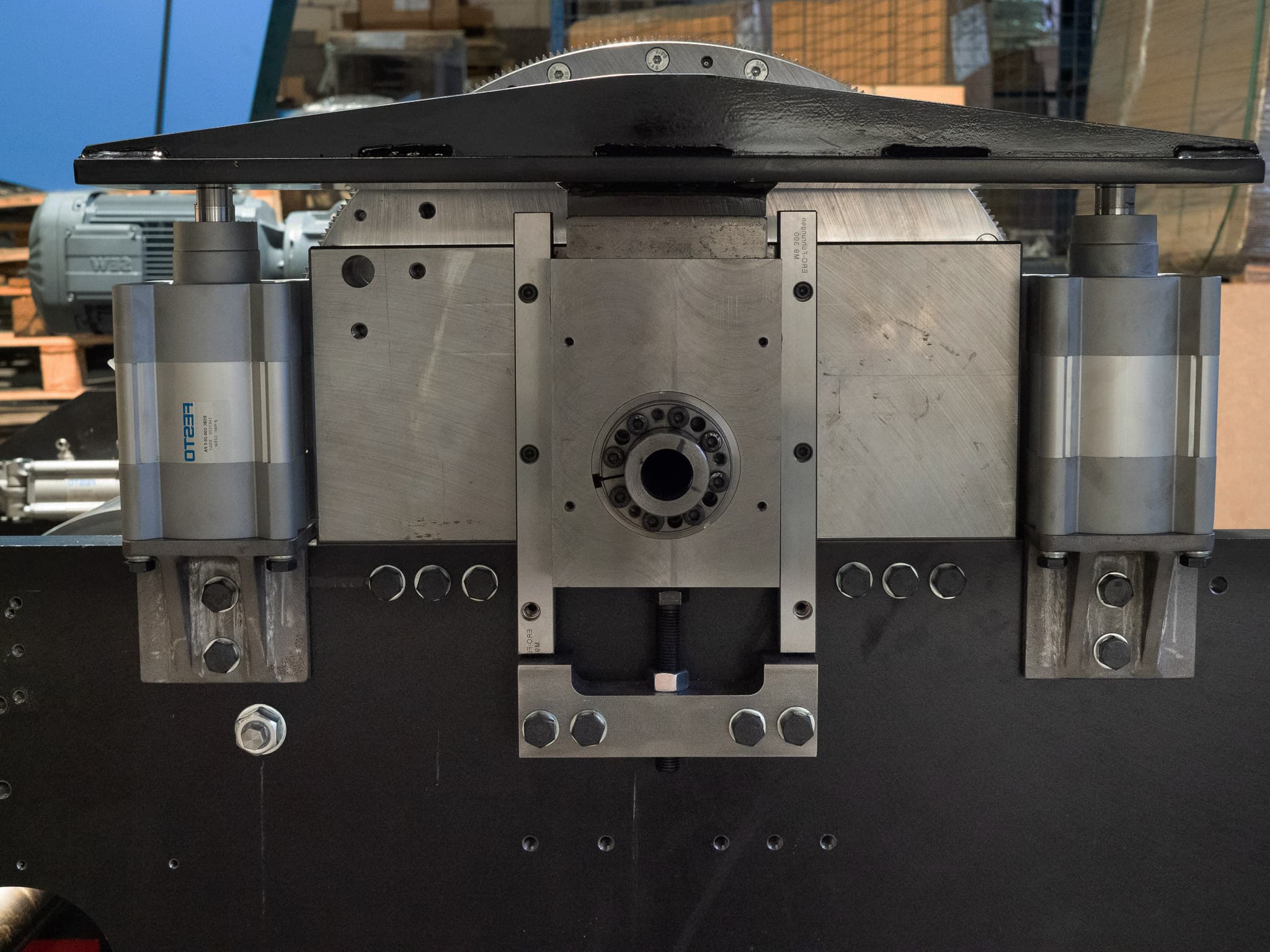
BENEFITS OF COLD CORRUGATION
Cold corrugation is a revolutionary energy-efficient solution for producing corrugated board that allows box makers to self-manufacture in short runs at their own facilities.
What are the benefits of cold corrugation?
Cold corrugation will streamline your business, simplify your supply chain and reduce your manufacturing costs. It brings a number of other competitive advantages:
Cold corrugation enables corrugation on demand, giving you complete control of your corrugated cardboard manufacturing process so you only produce as much board as you need. Cold corrugation also reduces energy consumption by as much as 60%. You save money, and reduce your carbon footprint, while your customers benefit from a ‘green’ low-carbon alternative to traditional corrugated board.
At only 14 metres long, the Interpac corrugator is straightforward to install and run, connecting to a standard 60 amp 3-phase power supply.
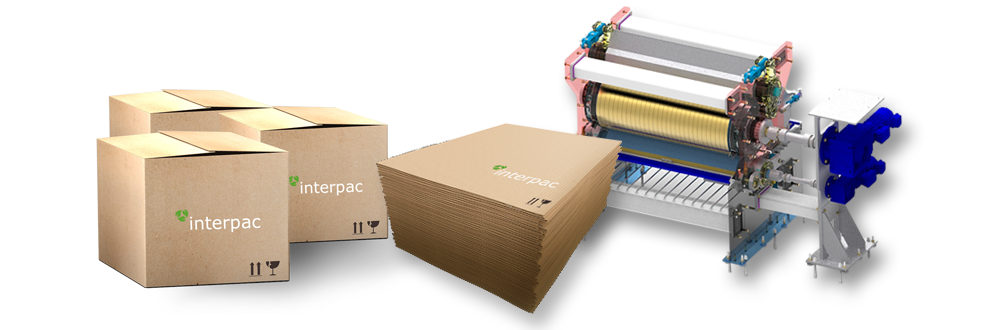
Make Significant Savings when you corrugate on demand
Take control of your corrugated cardboard manufacture and make significant cost savings of up to 30%. Cold corrugation promotes short-order, high-margin production with little-or-no waste. You only ever produce the board that you need.
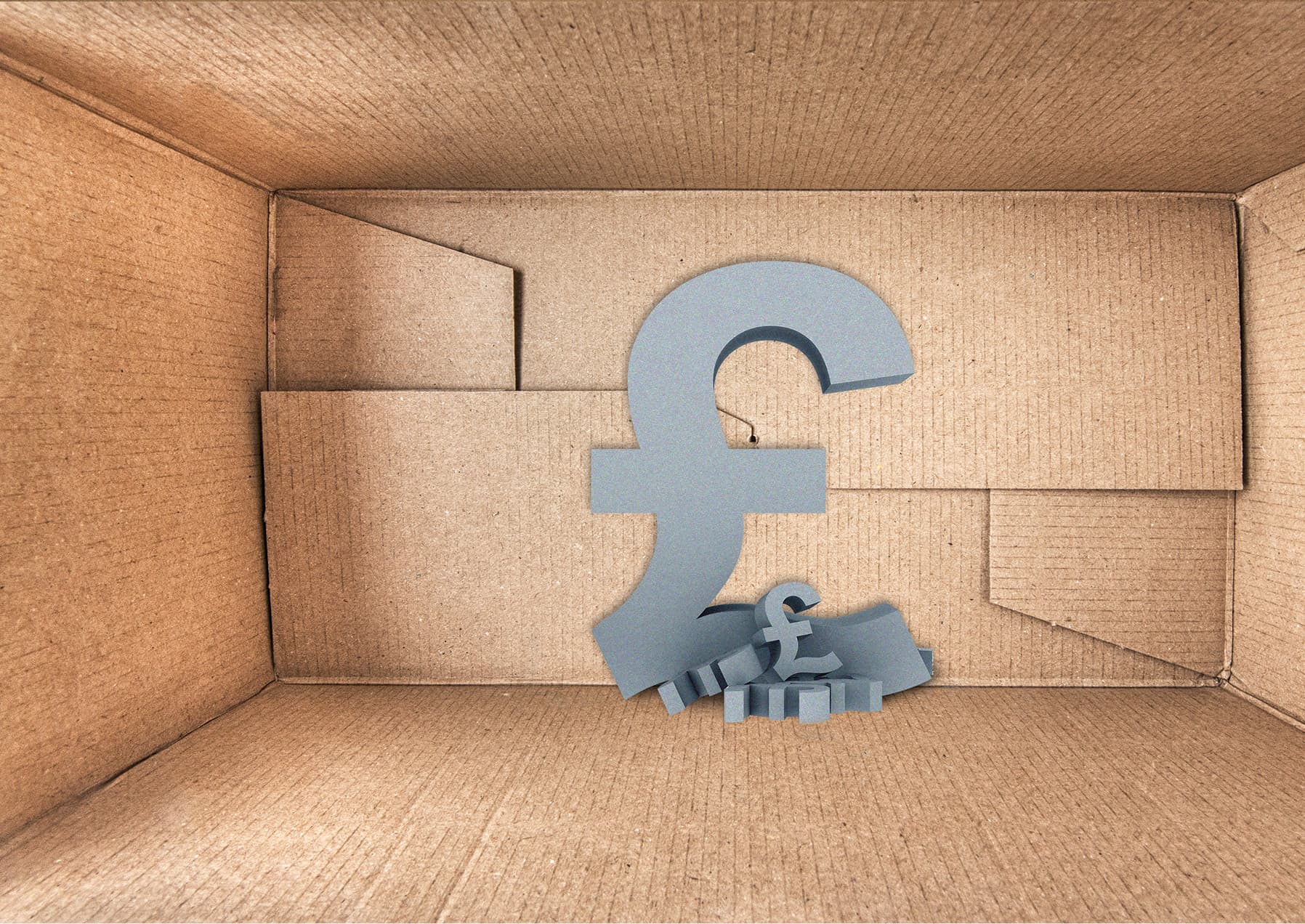
Use 90% Less Energy with cold corrugation
Companies around the world are striving to reduce their carbon footprint. The Interpac corrugator provides a sustainable alternative to traditional machines, cutting energy usage by as much as 60%. With the Interpac cold corrugator, you lower your carbon footprint and your customers benefit from a green, low-carbon alternative to traditional corrugated board.
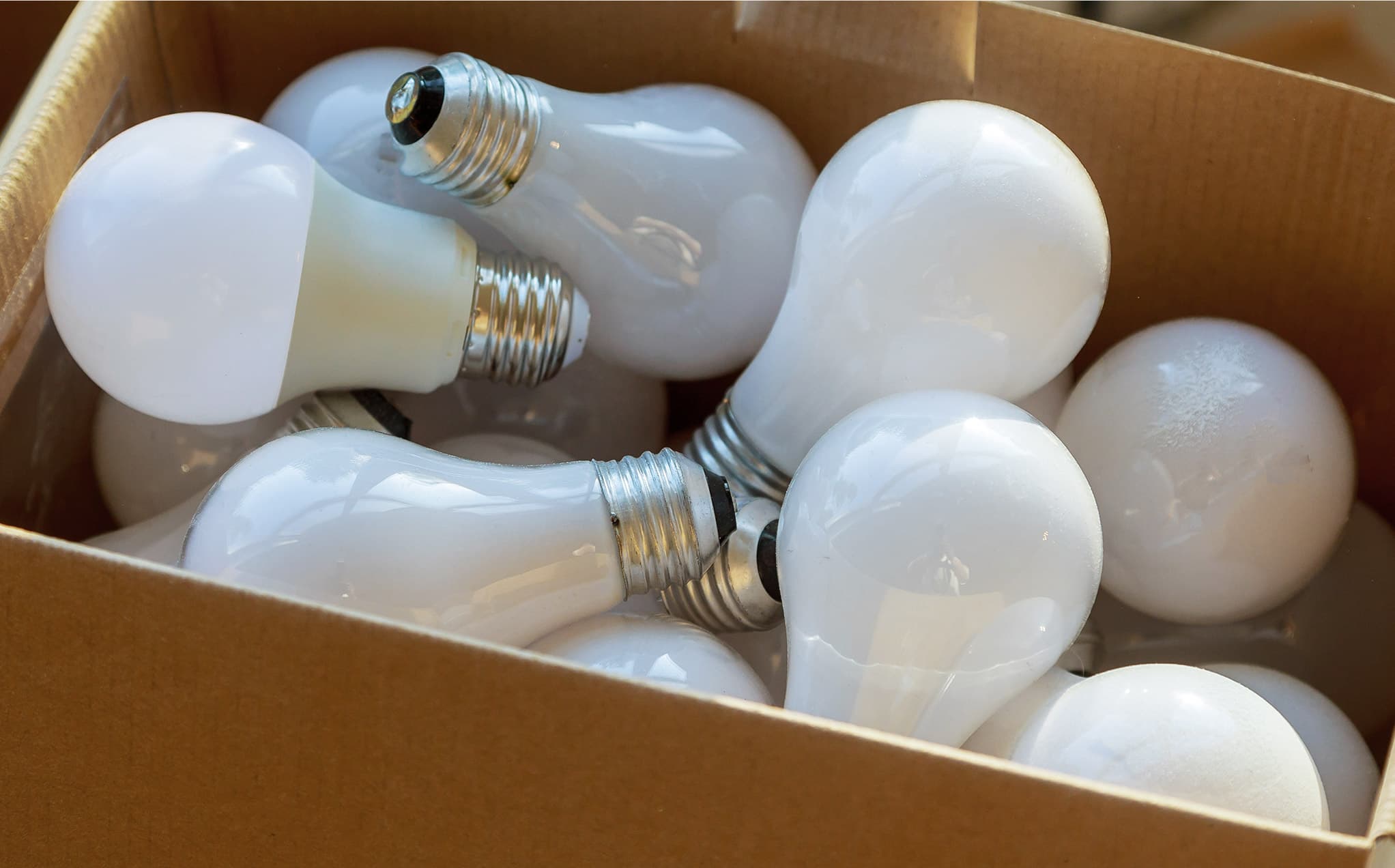
Box makers can make their own corrugated board on demand
Making corrugated board in-house, when you need it and in the quantities you really require, lowers costs and reduces waste. On-demand manufacturing allows you to make short production runs at your own premises, to start and stop whenever you want, and to have full control of your own production process.
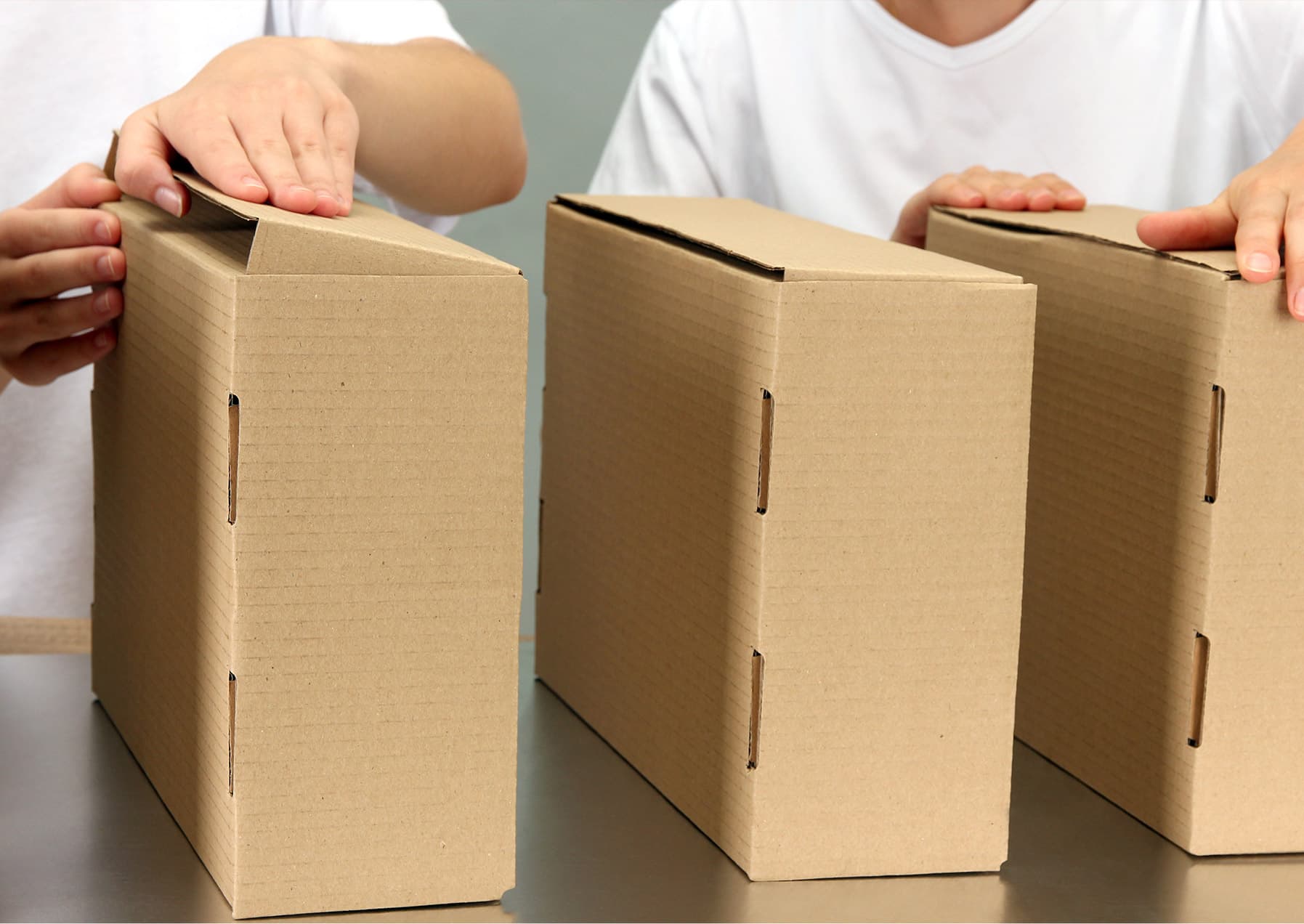
Cold corrugation significantly reduces the cost of ownership
With cold corrugation, you can install your own manufacturing plant at a fraction of the cost associated with traditional machines. Installation of a conventional corrugator typically costs up to £10 million. Prices for the Interpac cold corrugator are up to 70% less for a machine that can be as compact as you need it to be, starting at 29m long.
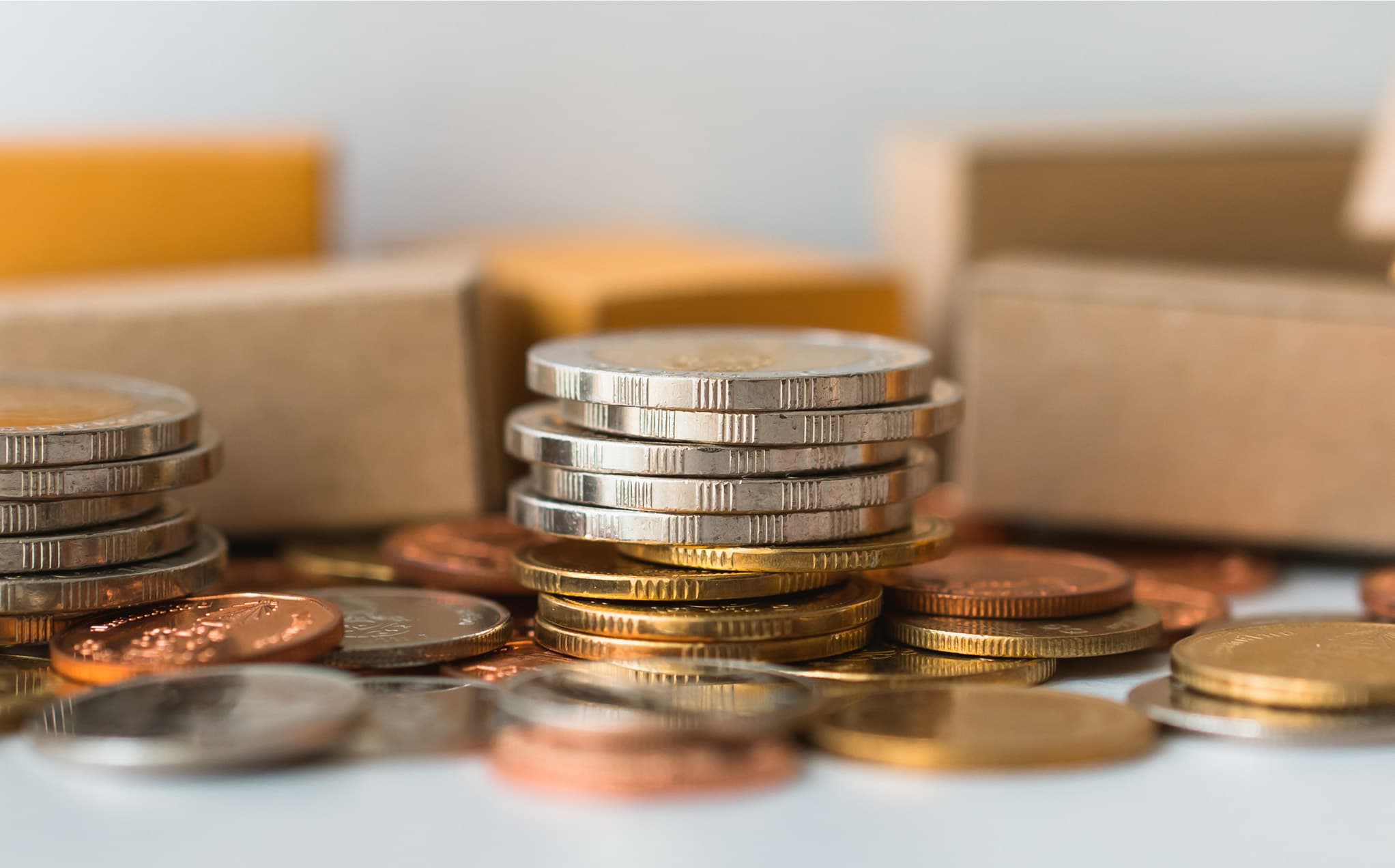
Cold corrugation does not use steam so saves on drying
The Interpac corrugator uses a steam-free cardboard manufacturing technique that eliminates the need for water removal during the manufacturing process. This simplifies production and reduces energy, space and cost.
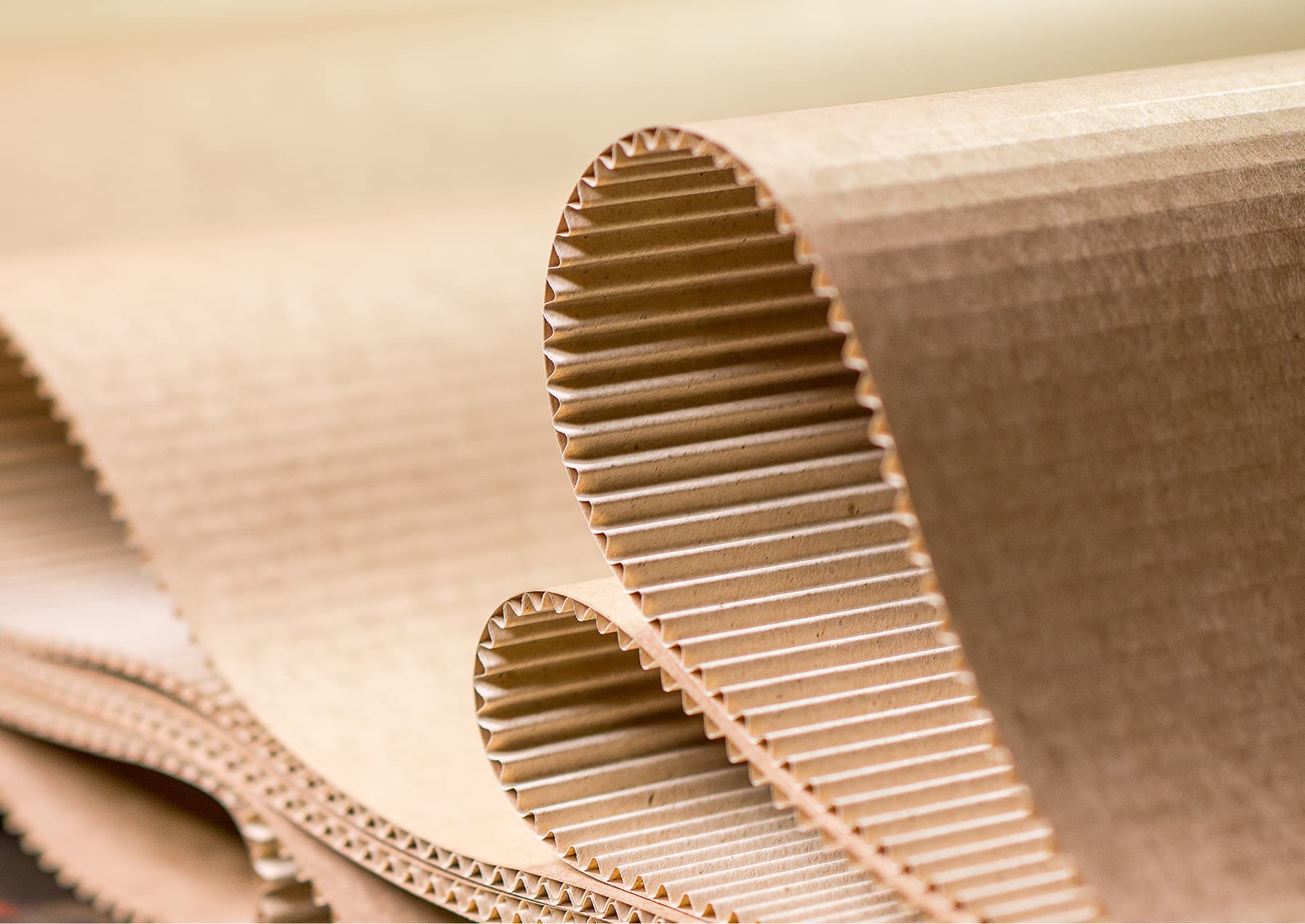
Cold corrugation creates stronger cardboard
Initial tests have shown that the revolutionary Interpac corrugator produces a stronger cardboard, weight-for-weight, than hot corrugation.
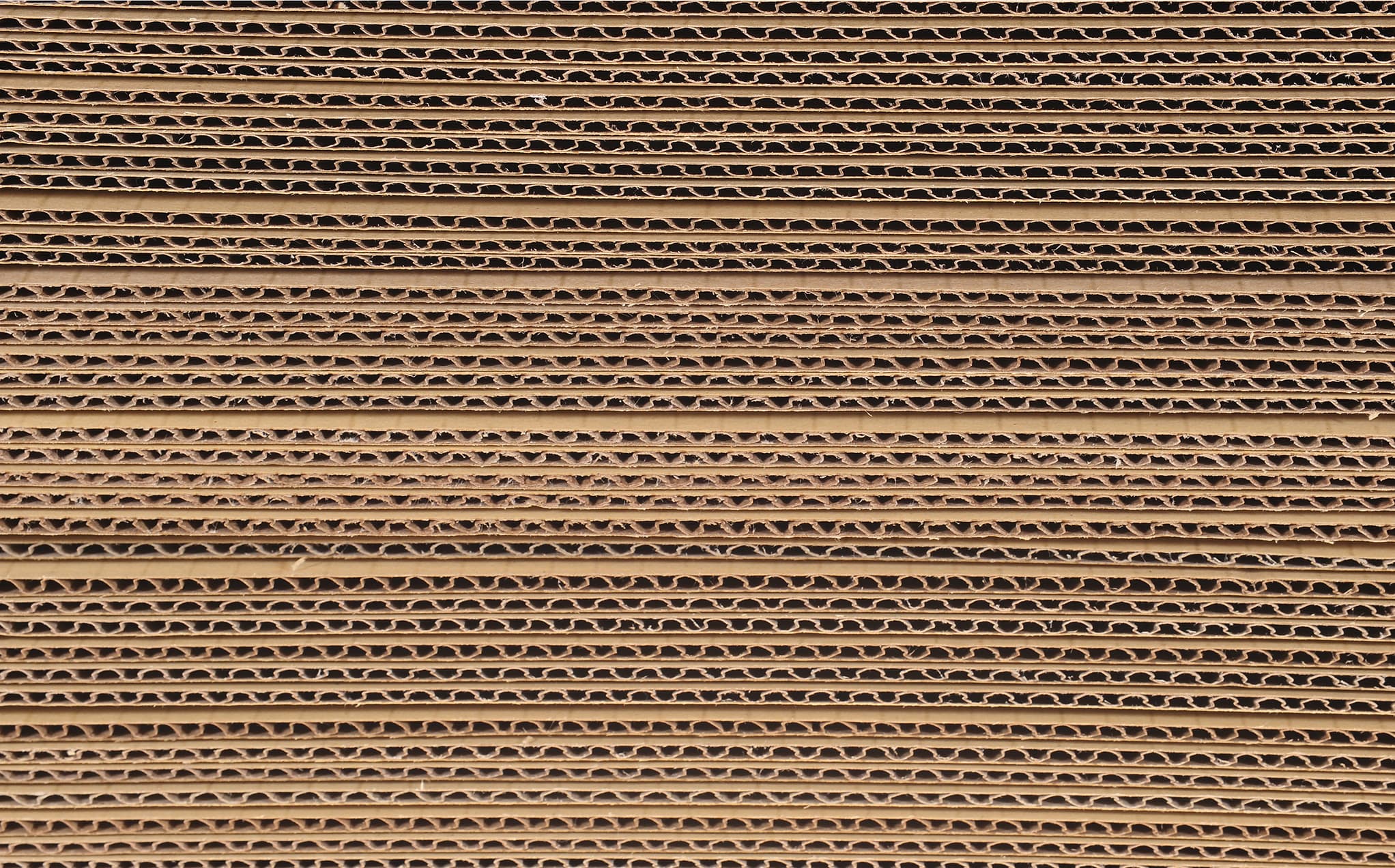
Self manufacturing reduces storage requirements
Sheet converters that purchase from corrugated board producers typically store large quantities of board. Storing paper reels for the purpose of self-manufacturing dramatically reduces warehouse space.
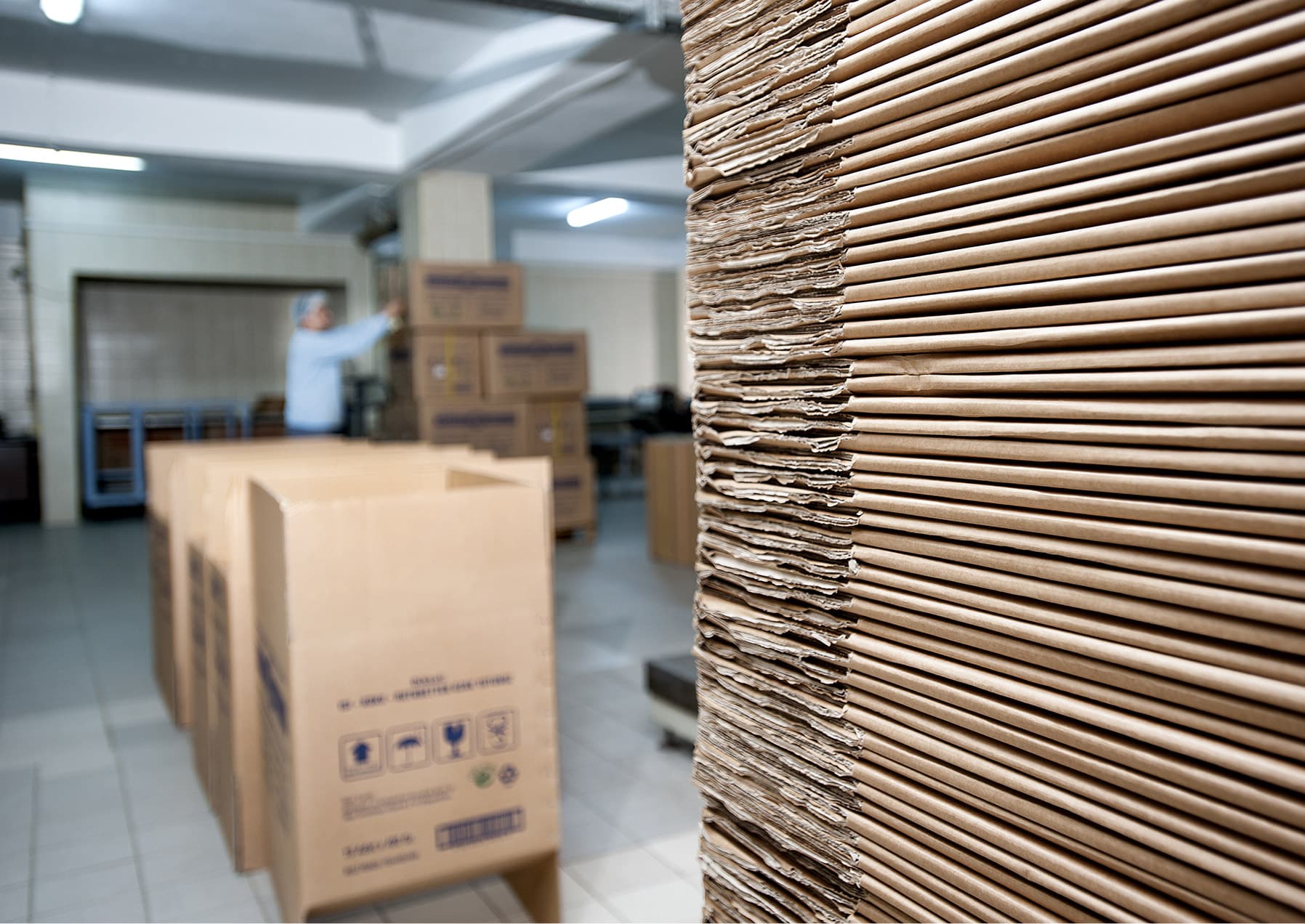
Since steam is not used in the manufacturing process, the surface of the board is smooth and flat. The industry is moving towards short-run, custom-printed boxes, and the Interpac corrugator allows for digital printing on a high-quality surface, which can be charged at a premium.
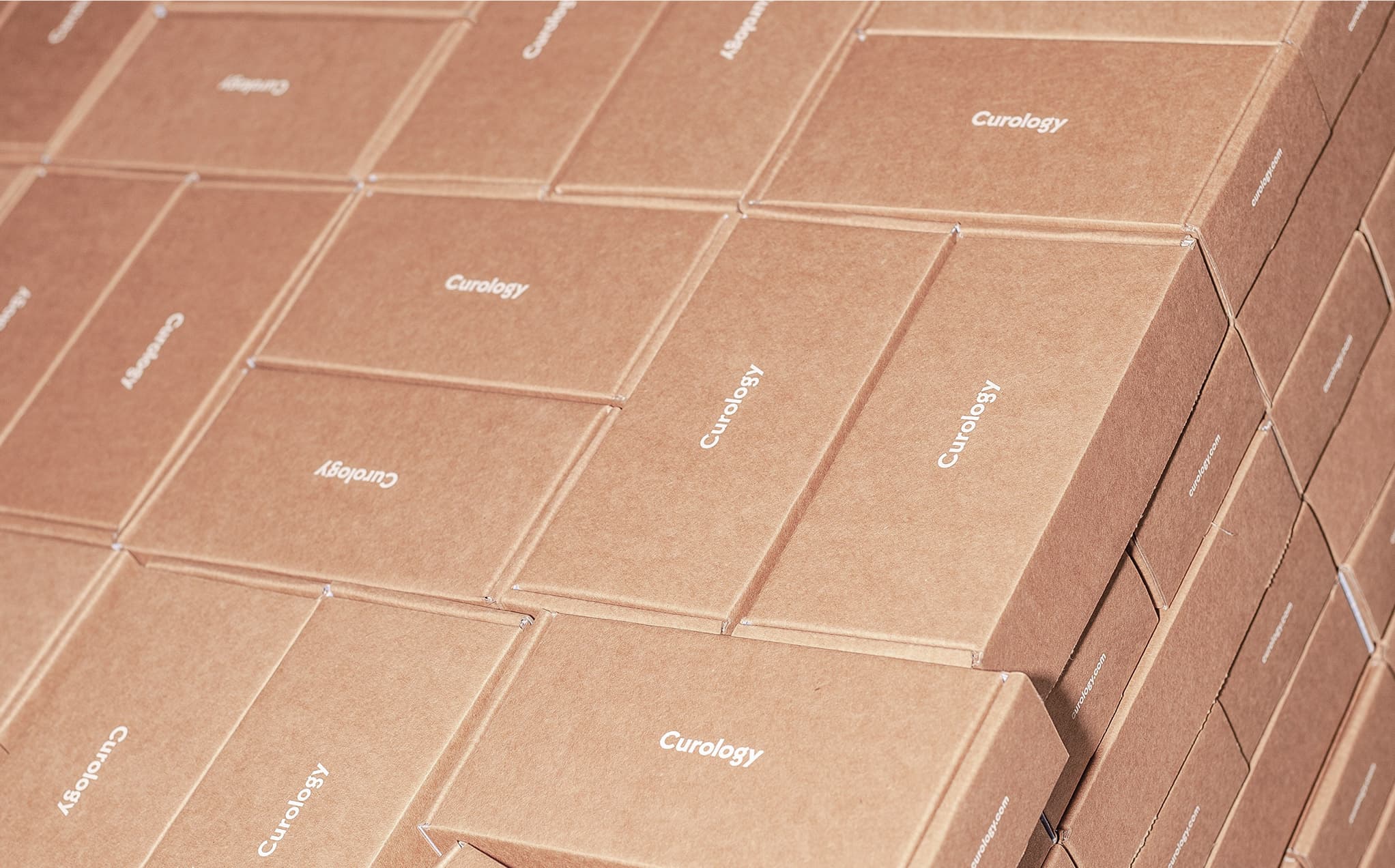